Today’s manufacturing industry demands a high level of precision, which is why several parts have to be custom-made. Due to technological developments, modern manufacturers can craft perfectly-tailored products that their manufacturing processes demand.
One technology that’s rapidly simplified the way manufacturers can do this is custom extrusion. Implementing this technology can result in a wide range of benefits, and many industries today are realizing these benefits and adopting this new development.
Table of Contents
What Is Custom Extrusion?
Custom extrusion has recently gained traction and, due to this, not many people know what exactly it is. It involves the manufacturing technique of creating products by pushing materials such as plastic and aluminum into a mold to manufacture a specific shape. As the name suggests, the process involves creating certain materials and shapes.
Typically, manufacturers use aluminum extrusion profiles due to their corrosion-resistant properties. While most extrusion is done with aluminum and plastic, manufacturers can also opt for polymers, clay, concrete, ceramics, etc.
This professional service transforms the raw material into custom shapes to meet individual specifications. In fact, due to its benefits, aluminum extrusion is currently growing at a CAGR of 5.1%.
Fabricators use a die with a particular profile and shape to create these custom objects. Custom extrusion demands a high level of skill from fabricators since the extrusion process depends on several variables, including the tolerance level, level of thickness, and the finishing.
Whether it’s continuous or semi-continuous, the length of the process depends on whether you have to manufacture a large quantity.
Types Of Custom Extrusion
While there are many kinds of extrusion you can consider, four types have primarily gained traction: micro, cold, friction, and hot custom extrusions.
Micro extrusion
This form of custom extrusion is relatively recent and involves creating micro-sized items through a die’s cross-section with a base material of just 1 mm. Such dies are complex to develop since they must be able to withstand immense pressure.
Cold extrusion
During this extrusion process, the material is forced through a die at or near room temperature. Cold extrusion requires specific material that comes in slugs and is poured into a die’s feeder, where they are joined together through the pressure to create a solid, custom object.
Cold extrusion is further divided into three categories:
- Backward extrusion: Used to create hollow shapes
- Forward extrusion: Use to create solid shapes
- Lateral extrusion: Used with liquids
Friction extrusion
This extrusion form is excellent at producing particle distributions in creating metal matrix composite materials and homogeneous microstructures. It involves automatically twisting metal slugs or billet based on a die’s position. When the die rotates, the metal-on-metal friction creates heat around the die’s entry. This heat eases the metal’s ability to pass through the die and create a custom shape.
Hot extrusion
In this form of custom extrusion, the material is passed through a high temperature and is forced into the die while it’s in a molten phase. While the temperature level depends on the kind of material used, it typically ranges from 650 Fahrenheit to even 1,300 Fahrenheit.
Getting the temperature right is a critical part of hot extrusion since the material may have issues moving through the die otherwise. Once the material is heated to the required temperature, hot extrusion serves as an excellent way to create specific products and components.
Benefits of Custom Extrusion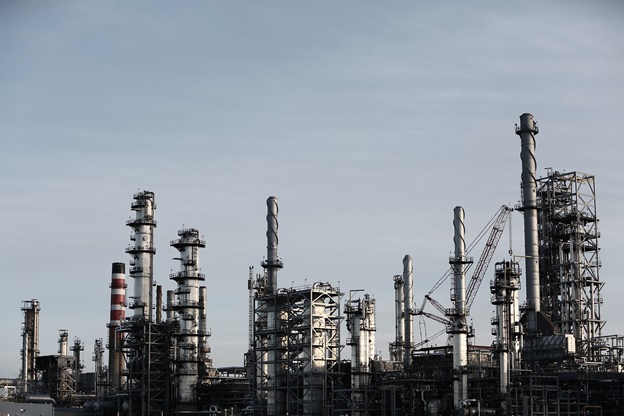
Custom extrusion can result in a variety of benefits for your manufacturing business. These include:
Lower costs
The cost of custom extrusion is lower than other types of molding. It results in efficiency, which leads to economies of scale, bringing down total costs.
Custom extrusion allows consistency since you can manufacture more products by putting in the same amount of effort, thereby creating higher volumes.
Versatility
Custom extrusion offers a high degree of flexibility since it allows the use and creation of any material shape and provides room for minor alterations.
Additionally, you can also work with hard or soft surfaces and create products demanding exact specifications. The customization process isn’t just limited to these aspects since you can also control the final product’s hardness, thickness, and color.
Sustainability
Since custom extrusion could involve the production of products and components at a large scale, manufacturers need to do whatever they can to minimize their carbon footprint.
Most custom extrusion processes involve using aluminum, which is quite environmentally-friendly since it can be recycled repeatedly without losing any of its properties. Apart from this, its resources aren’t, and processing aluminum demands relatively low levels of energy.
Diversity
Custom extrusion offers endless manufacturing opportunities due to the wide range of products it can manufacture. It can create simple tubes, wires, and rods, amongst other things, and can accommodate numerous shapes and sizes, such as hollow, solid, or intricate products.
Today, It is widely being used by many industries, including the pharmaceutical, automotive, and food production industries. Without this technology, it wouldn’t be possible to create specific products these industries demand. The technology gives way to new product innovations, such as ready-to-eat snacks, automobiles, and pharmaceutical solid oral doses.
Final thoughts
Custom extrusion has remarkably changed the manufacturing industry by defying limitations and creating high precision products at low costs and greater volumes. These developments have simplified the manufacturing process and made it more efficient than ever.
In fact, you’d be surprised how many products you use nowadays are manufactured with custom extrusion. If you’re currently looking for ways to up your manufacturing game, then custom extrusion is definitely something you need to consider.